Electroplating & Plating Chiller
Contents Table
▷ 6.What Are the Differences Between Electroplating Scroll Chiller and Electroplating Screw Chiller?
7.1 Compressor
7.2 Evaporator
7.3 Water Pump
7.4 Condenser
7.5 Controller Panel
What Are The Applications of an Electroplating Chiller?
|
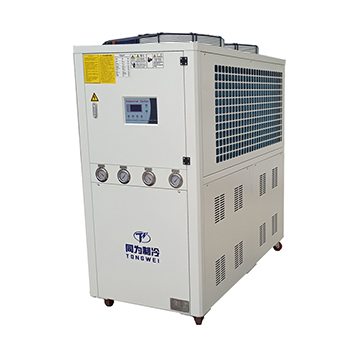
Electroplating Chiller
4.Why Need A Chiller For Electroplating &Plating Processing?
5.What’s the Difference Between Air-cooled & Water-cooled Electroplating Chillers?
Water-cooled Electroplating chillers use water from an external water cooling tower to dissipate heat from the brewing processes. These systems are longer lifespan, Relatively quiet, and more consistent cooling performance than the air-cooled Electroplating chiller.
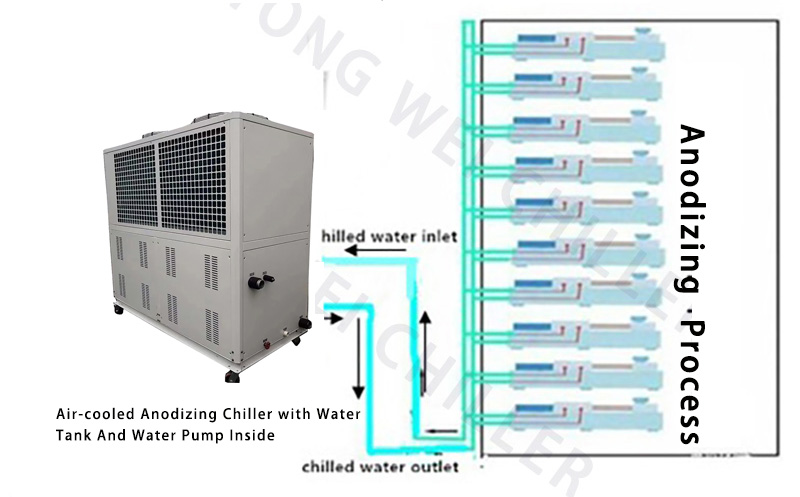
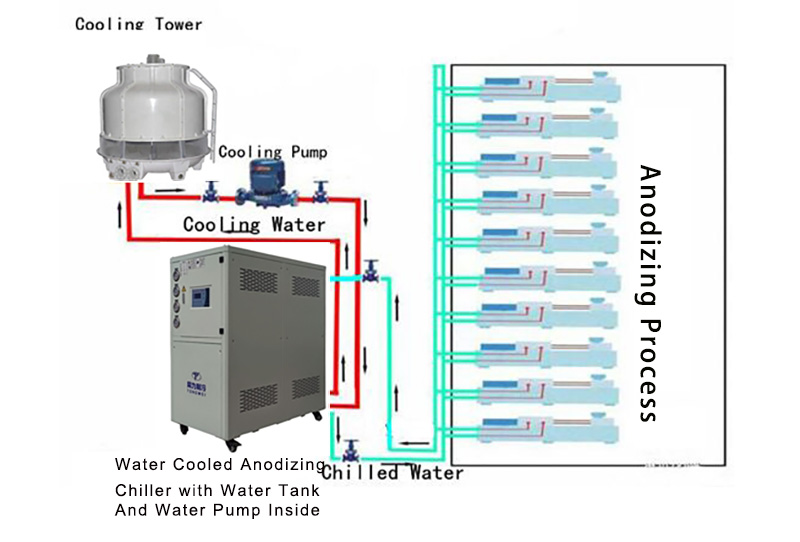
Electroplating Scroll Chiller Electroplating Screw Chiller
▪1/2 HP-60HP Above 60HP
▪ Danfoss/Panasonic Scroll Compressor Hanbell/Bitzer Screw compressor
▪Built with water tank and water pump Without water tank and water pump
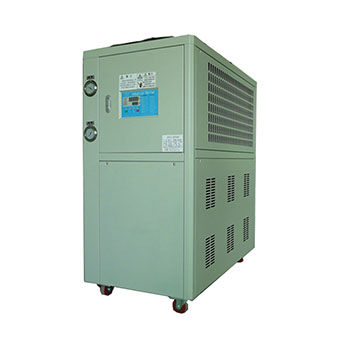
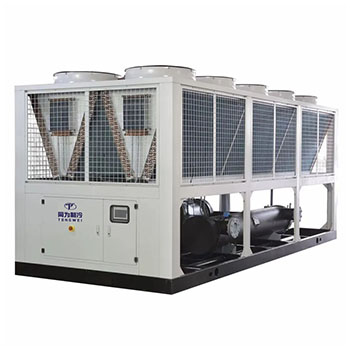
Air-cooled Electroplating Scroll Chiller Air-cooled Electroplating Screw Chiller
▪Packaged Chiller
7.What Are The Main Components of Electroplating Chillers?
Above 60HP Electroplating chiller,which is with Hanbell or Bitzer screw compressor;
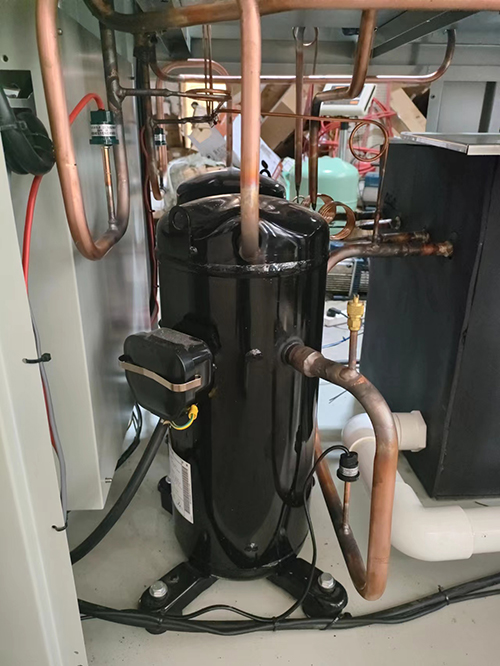
Panasonic Compressor
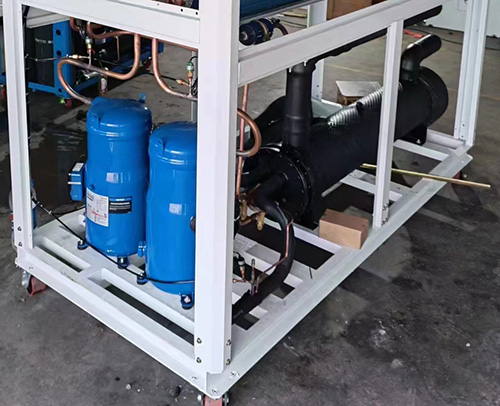
Danfoss Compressor
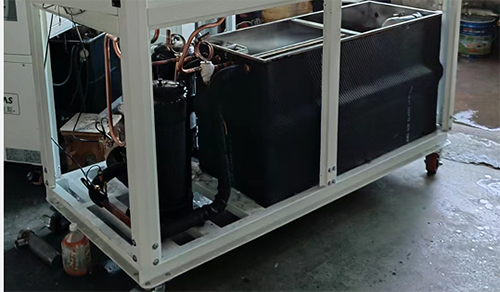
Coil in SS Water Tank Evaporator
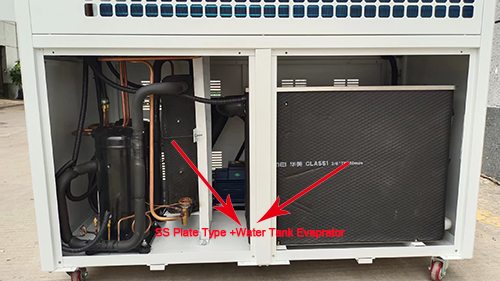
SS Plate Type+ Water Tank Evaporator
7.3 Water Pump
The water pump is designed to increase the pressure and the flow of the chilled water in a closed space.
ElectroplatingChiller is used with 304 Stainless Steel Water pump.
Water Pump
7.4 Condenser
The condenser for air-cooled Electroplating cooler is equipped with efficient cross-seam fins and female threaded copper tubes for high heat exchange efficiency and good stability.Its function is to cool down the refrigerant steam released from the compressor into a liquid or gas-liquid mixture.
Aluminum fin+fan Condenser for air -cooled Electroplating chiller
The condenser for water-cooled Electroplating cooler is shell and tube ,with the internal copper tubes employing an outer thread embossing process.This design effectively enhances the heat exchange efficiency between the refrigerant and water during the process. Compared to traditional smooth copper tubes, the outer thread embossing process increases the surface area of the copper tubes, thereby expanding the contact area for heat exchange and improving the thermal conductivity of the condenser. This optimization design allows the condenser of the water-cooled chiller to transfer heat from the refrigerant to the water more rapidly and consistently, enabling the water to carry away the heat.
Shell and tube Condenser for water-cooled Electroplating chiller
7.5 Controller Panel
Water chillers use precision digital temperature controller, it RS485 communication port,which can do remote monitoring and control. Simple operation, low failure rate, high safety factor, easy installation.
Controller Panel
▪ Chilled 0utlet water temperature control 7℃ to 25℃
9.What Are The Applications of an Electroplating Chiller?
Electroplating cooling systems are known for their specific temperature regulation capabilities and heat dissipation. Its main applications are as follows:
▪ Laser Cooling
▪ Plating
▪ Electroplating
▪ Impregnation
▪ Powder Coating
▪ Metal Coating
▪ Titanium Electroplating
▪ Quench Cooling
▪ Commercial Electroplating
▪ Spot Welding
▪ Furnace Cooling
▪ Cooling for Induction furnace
▪ Chromic Acid Electroplating
▪Die Casting
Our Electroplating chiller can accommodate other types of equipment as well. If you don‘t have your application here, please contact us for knowing more about.
10.What Are Advantages of an Electroplating Chiller for Your Electroplating &Plating Processing?
Material is anodized for several reasons, to ensure that anodized materials become more durable and long-lasting while expanding the range of applications they can be used for. Listed below are the main reasons why metals are anodized.
Improve corrosion resistance
Materials that will be used in high humidity/water contact environments benefit from Electroplating their metal components. For example, ships and hulls, petroleum facility platform superstructures, and terminal equipment all require Electroplating to be sufficient to provide a corrosion-resistant coating.
Hardening and Abrasion Control
After metal is anodized, its strength properties can be significantly improved. Unoxidized aluminum (in its non-anodized state) is soft and not suitable for applications that require reinforced components. In contrast, the resulting high tensile strength is valued and used in the manufacture of wear-resistant aluminum alloys.
Equipment Protection
Some industrial processes that emit heat such as Electroplating and electroplating processes, are protected from thermal damage. The chilling effect makes electrochemical cells and rectifiers durable by discarding all extra heat.
11. What Application Does A Electroplating Chiller Used In?
Electroplating Chillers are widely used in many application ,some as below:
Decorative Finishes: Electroplating is often used to give objects an attractive and reflective surface. For example, gold, silver, and chrome plating are used in jewelry, tableware, and automotive parts.
Anti-corrosion: A layer of corrosion-resistant metal (such as zinc) can be electroplated on objects made of non-corrosion-resistant materials to increase their service life.
Conductivity: Electroplating can improve the conductivity of materials. For example, copper plating is used in the electronics industry.
Engineering and Manufacturing: Electroplating is used in industries such as aerospace, automotive and medical device manufacturing to provide components with specific properties such as wear resistance, hardness and lubricity.
Printed circuit boards (PCBs): Electroplating is a key step in manufacturing PCBs, where copper is plated onto the surface to create conductive traces.
Jewelry and Fashion Accessories: Electroplating is widely used in the jewelry industry to coat base metals with a layer of gold or silver, creating a more affordable solid alternative to precious metals.
12.How to Choose Right Electroplating Chiller for Your Electroplating Process?
Cooling Capacity(kw)= Flow Rate(m3/h)*Temp Change(T1-T2)/0.86
Heat Load= C(specific heat)* M(quality output per hour )*Temp Change(T1-T2)
Water Flow Rate = 5 m³/hour
There are two types of chiller :Air Cooled Electroplating Chiller and Water Cooled Electroplating Chiller.
But Most customers use air cooled Electroplatingchiller ,which is more easily install and save space.
13.Get a Quote on Industrial Electroplating Chillers Now
As a leading industrial chiller manufacturer,we engineer and produce high-quality process chillers compatible with a broad range of industrial processes.
Depending on your needs, we also offer custom chillers to ensure that each client receives the industrial chiller best suited to their unique process.
Request a quote now on our Electroplating water chillers or learn about the other air-cooled chillers and water-cooled chillers.