Food Processing Chiller
Our chillers and cooling systems remove ice during food processing. Whether you are spending too much ice cooling your process, or ice is forming in your current chillers, our food processing chillers are a reliable and economical option to keep your products safe and delicious. We often design custom food processing cooling systems to meet the specific needs of an operation. With a wide range of capacities and system configurations, our food processing industry chillers are reliable and provide precise temperature control to meet your most demanding refrigeration and cooling needs.
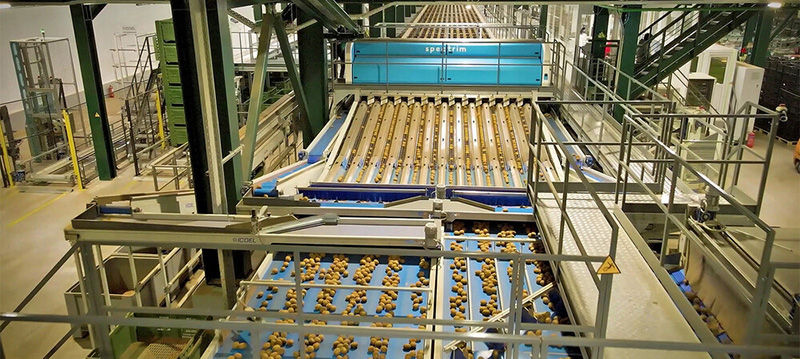
Food Processing
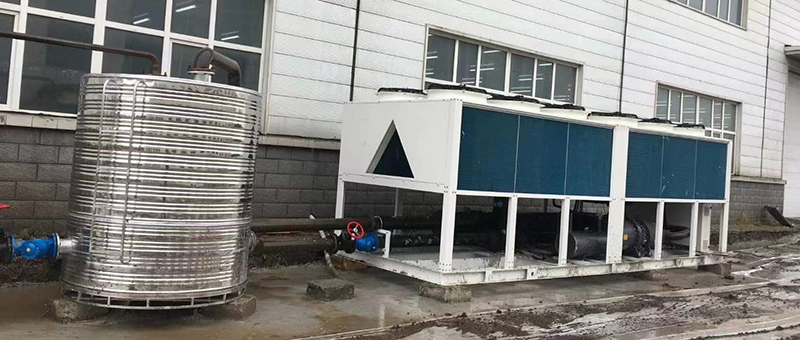
80 Ton AirCooled Screw Food Process Chiller
Water-cooled Food Processing chillers use water from an external water cooling tower to dissipate heat from the brewing processes. These systems are longer lifespan, Relatively quiet, and more consistent cooling performance than the air-cooled Food Processing chiller.
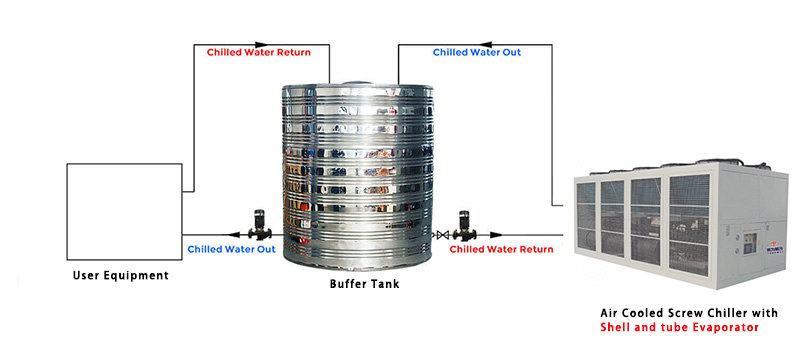
Air-cooled Food Processing Chiller Installation Drawing
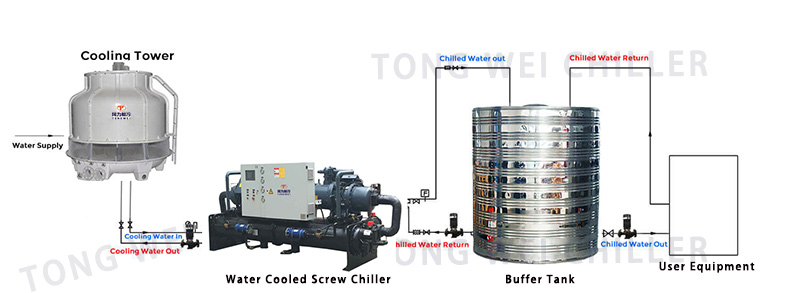
Water-cooled Food Processing Chiller Installation Drawing
4.What is the Difference Between Food Processing Scroll Chiller and Food Processing Screw Chiller?
Food Processing Scroll Chiller Food Processing Screw Chiller
▪1/2 HP-60HP(2KW-170KW) Above 60HP(Above 170KW)
▪ Danfoss/Panasonic Scroll Compressor Hanbell/Bitzer Screw compressor
▪Built with water tank and water pump Without water tank and water pump
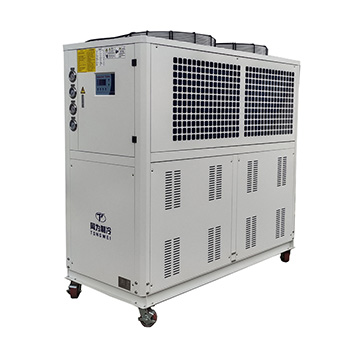
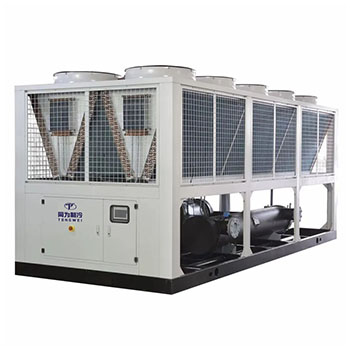
Air-cooled Food Processing Scroll Chiller Air-cooled Food Processing ScrewChiller
5.What Are The Main Components of Food Processing Chillers?
Above 80HP(70 Ton) Food Processing chiller , which is with Hanbell or Bitzer brand Screw compressor ,
These brand compressors are with high refrigeration efficiency,low noise ,energy saving,environmental protection and durability,safety and stability.
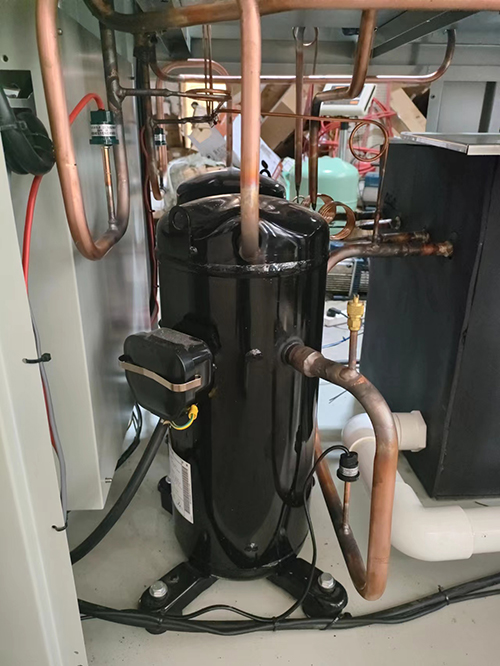
Panasonic Compressor
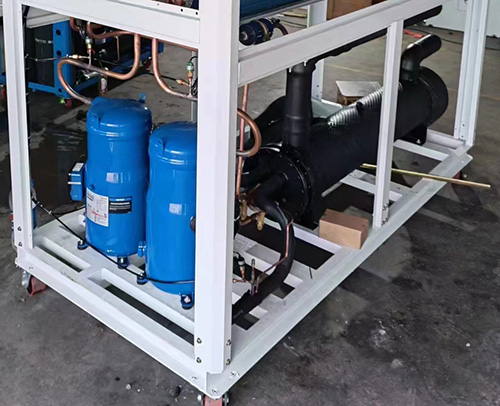
Danfoss Compressor
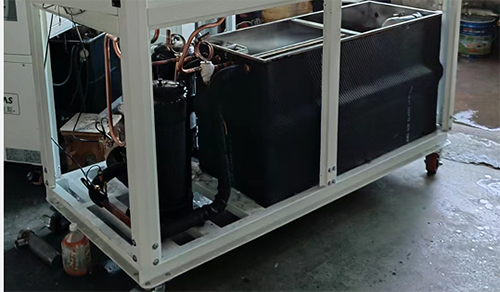
Coil in SS Water Tank Evaporator
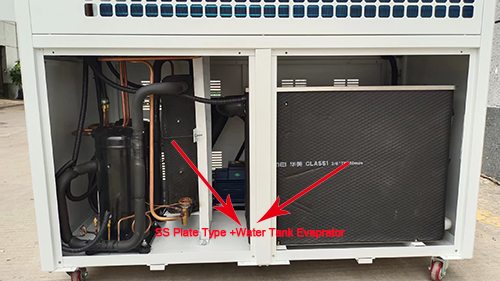
SS Plate Type+ Water Tank Evaporator
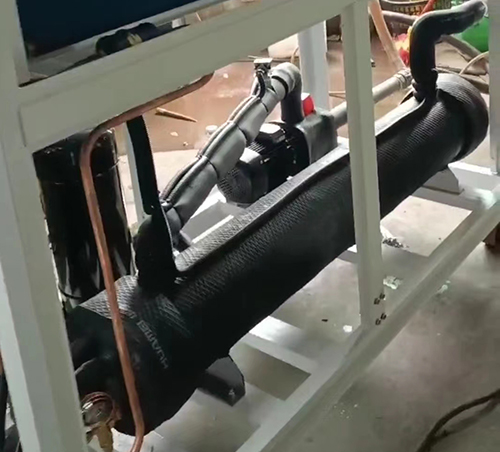
Shell and Tube Evaporator
5.3 Water Pump
The water pump is designed to increase the pressure and the flow of the chilled water in a closed space.
Water Pump
High Pressure Water Pump
5.4 Condenser
The condenser for air-cooled Food Processing chiller is equipped with efficient cross-seam fins and female threaded copper tubes for high heat exchange efficiency and good stability.Its function is to cool down the refrigerant steam released from the compressor into a liquid or gas-liquid mixture.
Aluminum fin+fan Condenser for air -cooled brewery chiller
The condenser for water-cooled Food Processing chiller is shell and tube ,with the internal copper tubes employing an outer thread embossing process.This design effectively enhances the heat exchange efficiency between the refrigerant and water during the process. Compared to traditional smooth copper tubes, the outer thread embossing process increases the surface area of the copper tubes, thereby expanding the contact area for heat exchange and improving the thermal conductivity of the condenser. This optimization design allows the condenser of the water-cooled chiller to transfer heat from the refrigerant to the water more rapidly and consistently, enabling the water to carry away the heat.
Shell and tube Condenser for water-cooled brewery chiller
5.5 Controller Panel
Food Processing chillers use precision digital temperature controller, it RS485 communication port,which can do remote monitoring and control. Simple operation, low failure rate, high safety factor, easy installation.
Controller Panel
6.Food Processing Chiller Coolants
Our industrial food processing chiller systems are available in two types: potable water and glycol. The difference between the two depends on the type of coolant used in the chiller.
The coolant in portable water chillers is water-based. With a double-walled heat exchanger, these food processing chillers prevent contamination. Best suited for medium temperature food processing such as cheese, meat and sauce production, potable water chillers are often an economical solution providing excellent cooling efficiency.
▪ Water-based coolant
▪ economy
▪ Anti-contamination Properties
▪ Suitable for medium temperature food processing
The coolant in a glycol chiller is a water-glycol mixture that acts as an antifreeze, helping achieve a lower freezing point than water. These chillers use non-toxic propylene glycol, as opposed to ethylene, to ensure food safety. Glycol chillers are often used in low-temperature storage applications for food products such as yogurt, ice cream, chocolate, and cold tables, but are also suited for above-freezing applications.
▪ Propylene glycol- and water mixture as coolant
▪ Antifreeze properties
▪ Consistent temperatures
▪ Zero product spoilage and improved food quality
How to calculate right cooling capacity for your Food Processing chillers?
Cooling Capacity(kw)= Flow Rate(m3/h)*Temp Change(T1-T2)/0.86
Heat Load= C(specific heat)* M(quality output per hour )*Temp Change(T1-T2)
Water Flow Rate = 5 m³/hour
There are two types of chiller :Air Cooled Food Processing Chiller and Water Cooled Food Processing Chiller.
Don’t delay in making the best decision for your manufacturing business and your future by increasing your production capabilities with an Food Processing chiller. Contact us today for more information on a Food Processing chiller.
Our probessional team will help you with any questions you have on our Food Processing chiller units. We look forward to hearing from you!