Blow Molding Chiller
Contents Table
6.1 Compressor
6.2 Evaporator
6.3 Water Pump
6.4 Condenser
6.5 Controller Panel
|
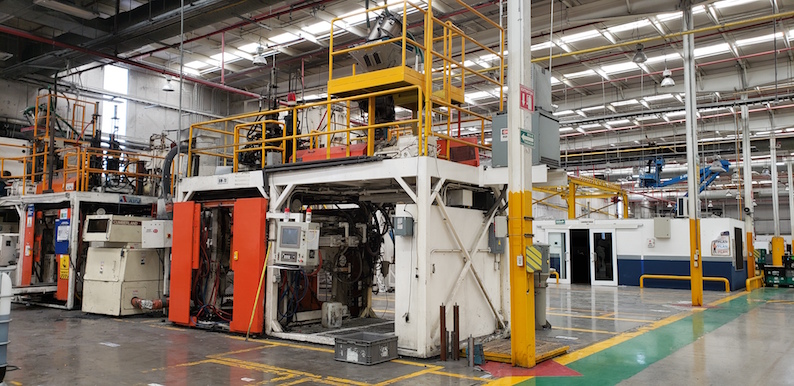
2.What Is Blow Molding Chiller?
A blow molding chiller is a specialized cooling machine used in the blow molding process, which is a manufacturing technique used to create hollow objects such as bottles, containers, and other plastic parts. This process involves heating a thermoplastic material (usually in the form of pellets or preforms) until it becomes pliable, then blowing air or other gas into it to create the desired shape within a mold.
A blow molding chiller is a cooling device designed to maintain precise and consistent temperatures in the molds, as well as in the plastic material itself. It accomplishes this by circulating a chilled liquid (typically water or a water-glycol mixture) through the mold and other components of the blow molding machinery.
Maintaining the correct temperature is critical for achieving the desired product quality, consistency, and structural integrity. If the plastic material is too hot or too cold during the molding process, it can lead to defects in the final product. The blow molding chillers help ensure that the plastic material is at the optimal temperature for forming the desired shape.
A blow molding chiller is an essential part in the blow molding process, which helping to regulate temperatures and improve the quality of the final plastic products.
4.What’s the Difference Between Air-cooled & Water-cooled Blow Molding Chillers?There are two types of Blow Moldingchiller: one is air-cooled Blow Molding chiller ,the other is water-cooled Blow Molding chiller ;
Water-cooled Blow Molding chillers use water from an external water cooling tower to dissipate heat from the brewing processes. These systems are longer lifespan, Relatively quiet, and more consistent cooling performance than the air-cooled Blow Molding chiller.
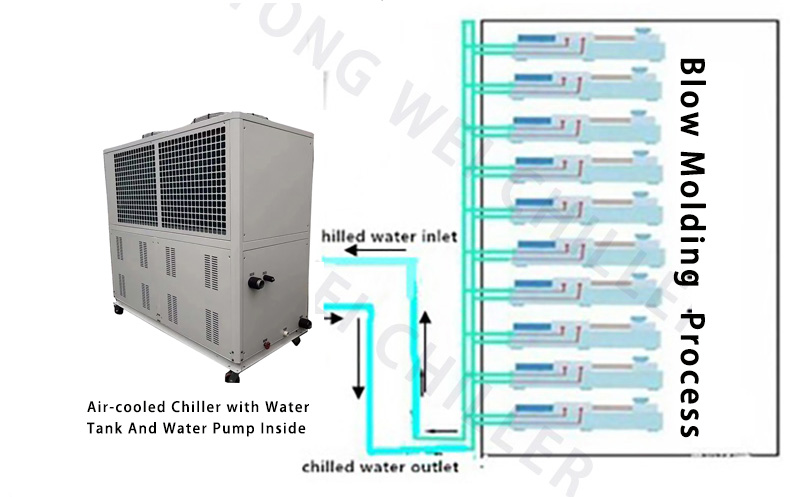
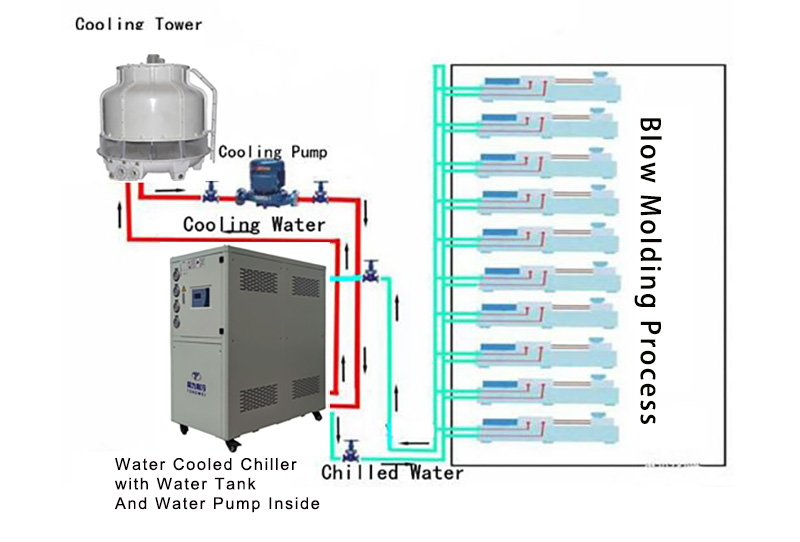
Blow Molding Scroll Chiller Blow Molding Screw Chiller
▪1/2 HP-60HP Above 60HP
▪ Danfoss/Panasonic Scroll Compressor Hanbell/Bitzer Screw compressor
▪Built with water tank and water pump Without water tank and water pump
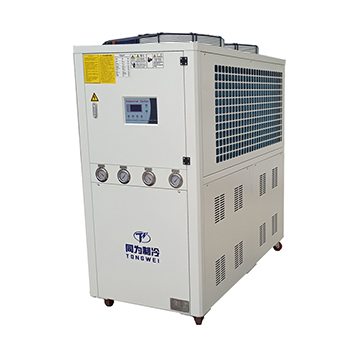
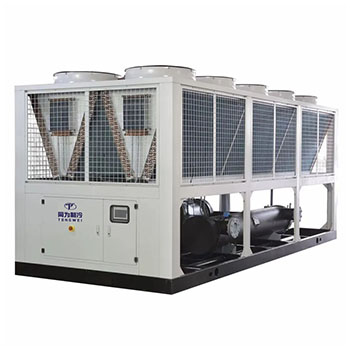
Air-cooled Blow Molding Scroll Chiller Air-cooled Blow Molding Screw Chiller
6.What Are The Main Components of Blow Molding Chillers?
Above 60HP Blow Molding chiller,which is with Hanbell or Bitzer screw compressor;
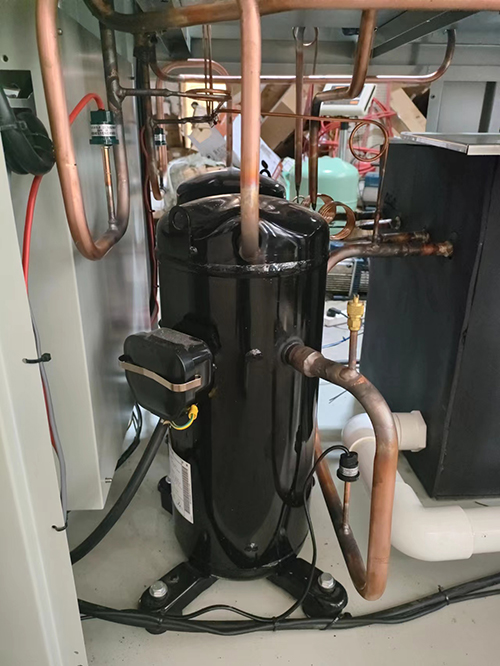
Panasonic Compressor
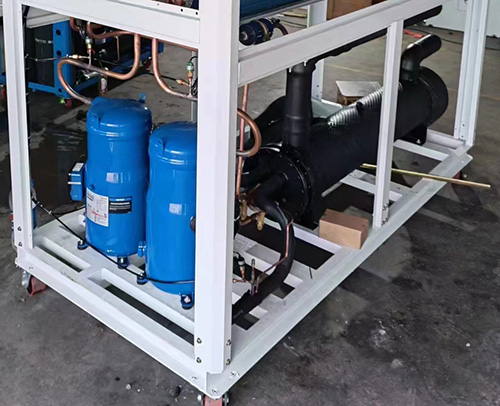
Danfoss Compressor
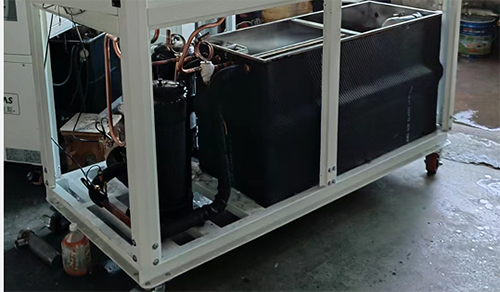
Coil in SS Water Tank Evaporator
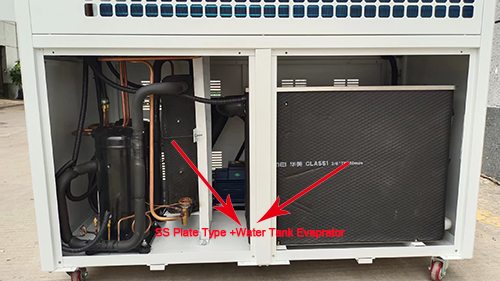
SS Plate Type+ Water Tank Evaporator
6.3 Water Pump
The water pump is designed to increase the pressure and the flow of the chilled water in a closed space.
Blow Molding Chiller is used with 304 Stainless Steel Water pump.
Water Pump
6.4 Condenser
The condenser for air-cooled Blow Molding cooler is equipped with efficient cross-seam fins and female threaded copper tubes for high heat exchange efficiency and good stability.Its function is to cool down the refrigerant steam released from the compressor into a liquid or gas-liquid mixture.
Aluminum fin+fan Condenser for air -cooled Blow Molding chiller
The condenser for water-cooled Blow Molding cooler is shell and tube ,with the internal copper tubes employing an outer thread embossing process.This design effectively enhances the heat exchange efficiency between the refrigerant and water during the process. Compared to traditional smooth copper tubes, the outer thread embossing process increases the surface area of the copper tubes, thereby expanding the contact area for heat exchange and improving the thermal conductivity of the condenser. This optimization design allows the condenser of the water-cooled chiller to transfer heat from the refrigerant to the water more rapidly and consistently, enabling the water to carry away the heat.
Shell and tube Condenser for water-cooled Blow Molding chiller
6.5 Controller Panel
Water chillers use precision digital temperature controller, it RS485 communication port,which can do remote monitoring and control. Simple operation, low failure rate, high safety factor, easy installation.
Controller Panel
8.How to Choose Right Blow Molding Chiller for Your Blow Molding Process?
Cooling Capacity(kw)= Flow Rate(m3/h)*Temp Change(T1-T2)/0.86
Heat Load= C(specific heat)* M(quality output per hour )*Temp Change(T1-T2)
Water Flow Rate = 5 m³/hour
There are two types of chiller :Air Cooled Blow Molding Chiller and Water Cooled Blow Molding Chiller.
But Most customers use air cooled Blow Moldingchiller ,which is more easily install and save space.
As a leading industrial chiller manufacturer,we engineer and produce high-quality process chillers compatible with a broad range of industrial processes.
Depending on your needs, we also offer custom chillers to ensure that each client receives the industrial chiller best suited to their unique process.
Request a quote now on our industrial plastic process chillers or learn about the other air-cooled chillers and water-cooled chillers.