Injection Molding Chiller
The plastics industry is one of the largest and most important industries in the world, affecting nearly every aspect of our lives, from food and medicine to entertainment and aerospace. Most plastic parts used every day are injection molded. Injection molding is a very efficient way to produce identical parts in batches with very little plastic. The injection molding machine heats the plastic pellets until they melt and then injects them into a forming mold, where the plastic parts cool. The cooling process can be lengthy; more than 80% of plastic manufacturing time is spent cooling. Injection molding chillers will significantly reduce cooling time and maintain product quality.
1.What is Injection Molding?
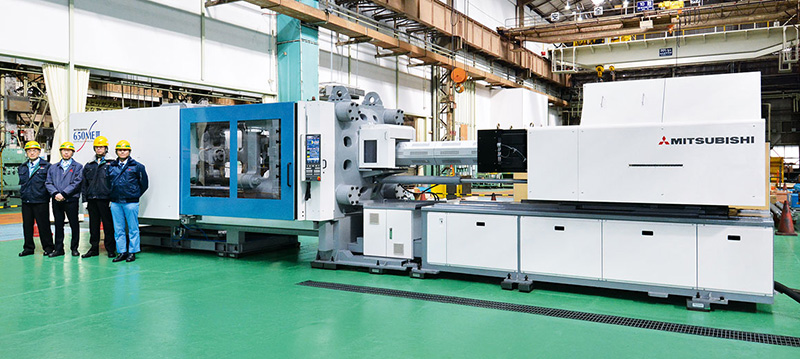
2.What is Injection Molding Chiller?
Injection molding chillers are specialized refrigeration systems used in the injection molding process. It plays a key role in maintaining precise and consistent temperatures in the mold and the hydraulic system of the injection molding machine. This is important for following reasons:
Temperature control: Controlling the temperature of the mold is key to producing high-quality plastic parts. Different plastics have specific temperature requirements for optimal flow and solidification. Injection Molding Chillers help keep these temperatures within a narrow range, ensuring consistent part quality.
Prevent warping and defects: Rapid and uneven temperature changes can cause plastics to warp, crack, or develop other defects. Injection molding chillers help prevent these problems by keeping molds at a stable and controllable temperature.
Improved cycle times: Maintaining precise temperatures cools and solidifies the plastic faster, which reduces cycle times and increases overall production efficiency.
Extended mold life: Temperature fluctuations can cause thermal stress on molds, which can lead to premature wear and damage. Injection molding chillers help extend the life of molds by providing consistent and controlled cooling.
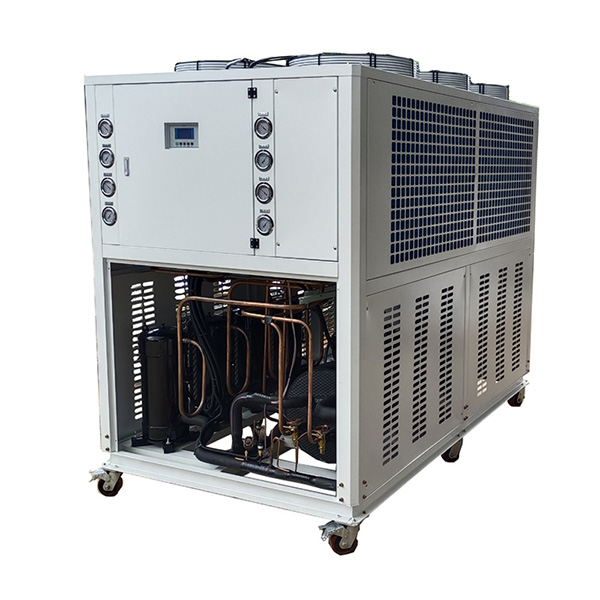
Injection Molding Chiller
4.What’s the Difference Between Air-cooled & Water-cooled Injection Molding Chillers?
There are two types of Injection Moldingchiller: one is air-cooled Injection Molding chiller ,the other is water-cooled Injection Molding chiller ;
Water-cooled Injection Molding chillers use water from an external water cooling tower to dissipate heat from the brewing processes. These systems are longer lifespan, Relatively quiet, and more consistent cooling performance than the air-cooled Injection Molding chiller.
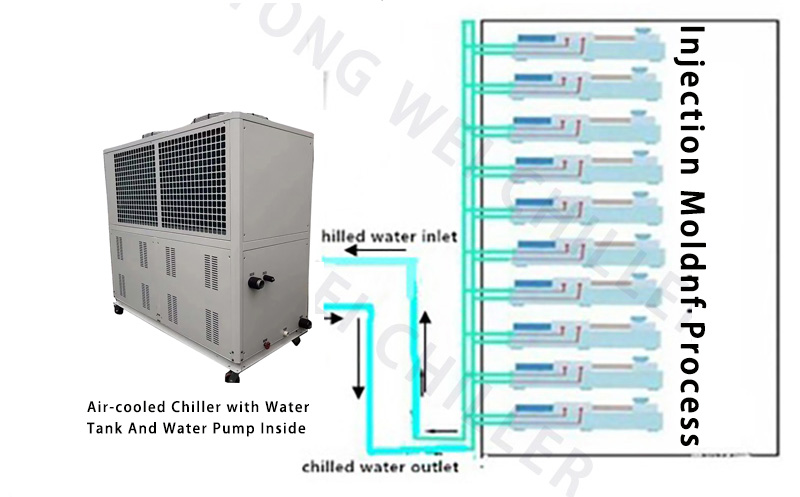
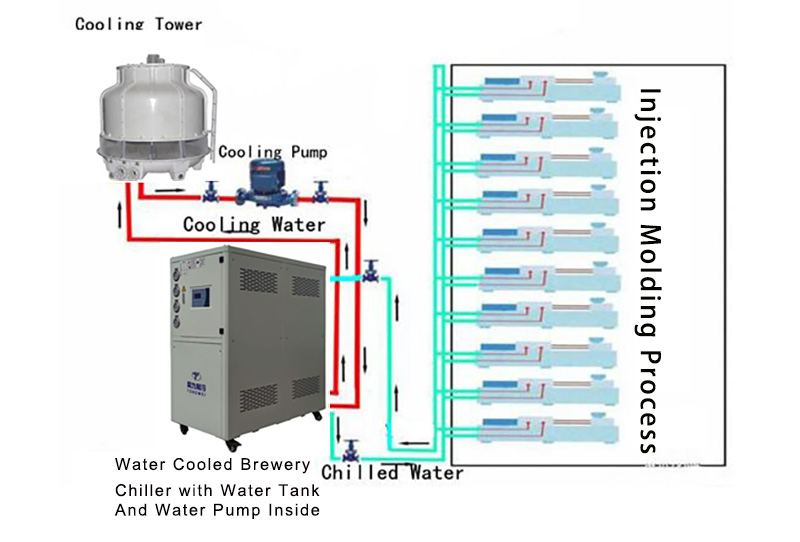
Injection Molding Scroll Chiller Injection Molding Screw Chiller
▪1/2 HP-60HP Above 60HP
▪ Danfoss/Panasonic Scroll Compressor Hanbell/Bitzer Screw compressor
▪Built with water tank and water pump Without water tank and water pump
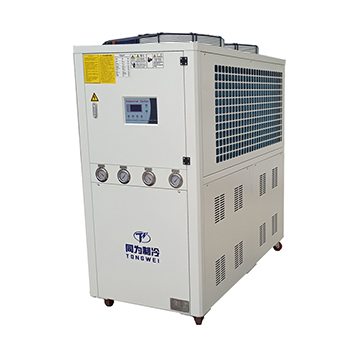
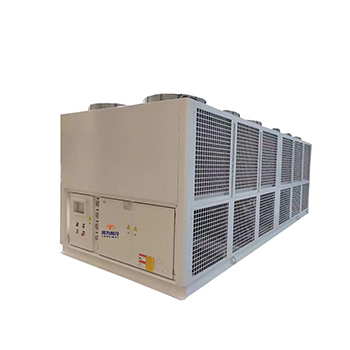
Air-cooled Injection Molding Scroll Chiller Air-cooled Injection Molding Screw Chiller
6.What Are The Main Components of Injection Molding Chillers?
Above 60HP Injection Molding chiller,which is with Hanbell or Bitzer screw compressor;
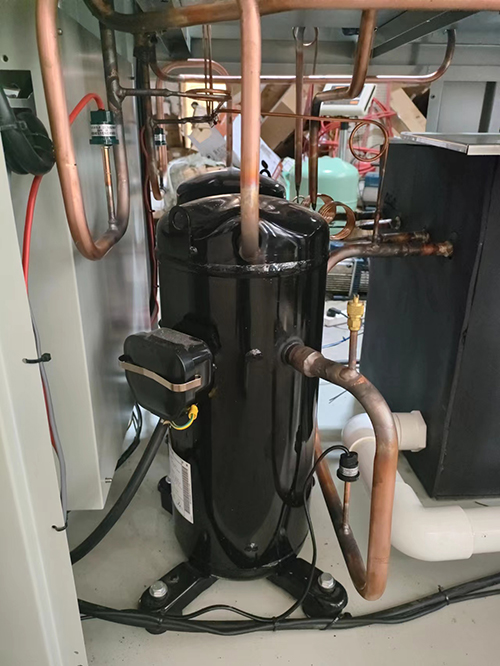
Panasonic Compressor
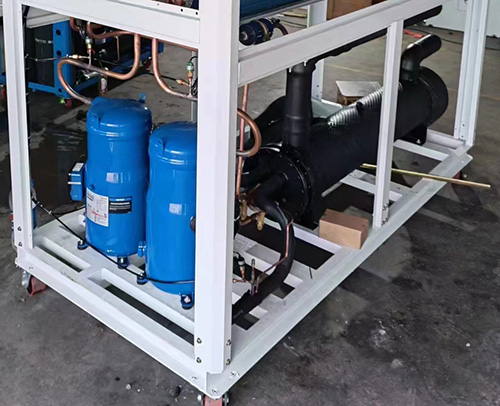
Danfoss Compressor
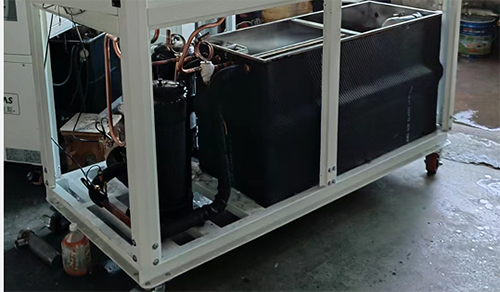
Coil in SS Water Tank Evaporator
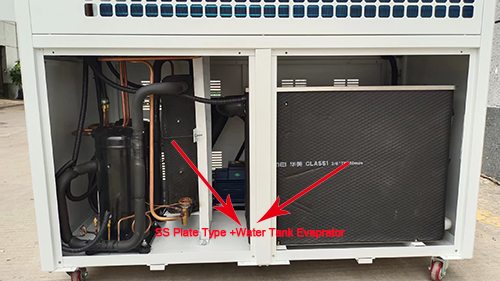
SS Plate Type+ Water Tank Evaporator
6.3 Water Pump
The water pump is designed to increase the pressure and the flow of the chilled water in a closed space.
Injection Molding Chiller is used with 304 Stainless Steel Water pump.
Water Pump
6.4 Condenser
The condenser for air-cooled Injection Molding cooler is equipped with efficient cross-seam fins and female threaded copper tubes for high heat exchange efficiency and good stability.Its function is to cool down the refrigerant steam released from the compressor into a liquid or gas-liquid mixture.
Aluminum fin+fan Condenser for air -cooled Injection Molding chiller
The condenser for water-cooled Injection Molding cooler is shell and tube ,with the internal copper tubes employing an outer thread embossing process.This design effectively enhances the heat exchange efficiency between the refrigerant and water during the process. Compared to traditional smooth copper tubes, the outer thread embossing process increases the surface area of the copper tubes, thereby expanding the contact area for heat exchange and improving the thermal conductivity of the condenser. This optimization design allows the condenser of the water-cooled chiller to transfer heat from the refrigerant to the water more rapidly and consistently, enabling the water to carry away the heat.
Shell and tube Condenser for water-cooled Injection Molding chiller
6.5 Controller Panel
Water chillers use precision digital temperature controller, it RS485 communication port,which can do remote monitoring and control. Simple operation, low failure rate, high safety factor, easy installation.
Controller Panel
8.How to Choose Right Injection Molding Chiller for Your Injection Molding Process?
There are two types of chiller :Air Cooled Injection Molding Chiller and Water Cooled Injection Molding Chiller.
But Most customers use air cooled Injection Moldingchiller ,which is more easily install and save space.
As a leading industrial chiller manufacturer,we engineer and produce high-quality process chillers compatible with a broad range of industrial processes.
Depending on your needs, we also offer custom chillers to ensure that each client receives the industrial chiller best suited to their unique process.
Request a quote now on our Film Blowing water chillers or learn about the other air-cooled chillers and water-cooled chillers.