Without proper temperature regulation, many heat-sensitive manufacturing processes will either deteriorate or result in changes to the finished product. Various types of industrial chillers can be widely used in metallurgy and industrial welding. Industrial welding chillers used for spot welding, MIG welding, TIG welding and other resistance welding,which can help improve product quality and process efficiency
We can also custom design and manufacture water chillers to meet your specific needs.If you need a waterjet cutting chiller for a different waterjet cutting process? Contact Us–we’re here to help.
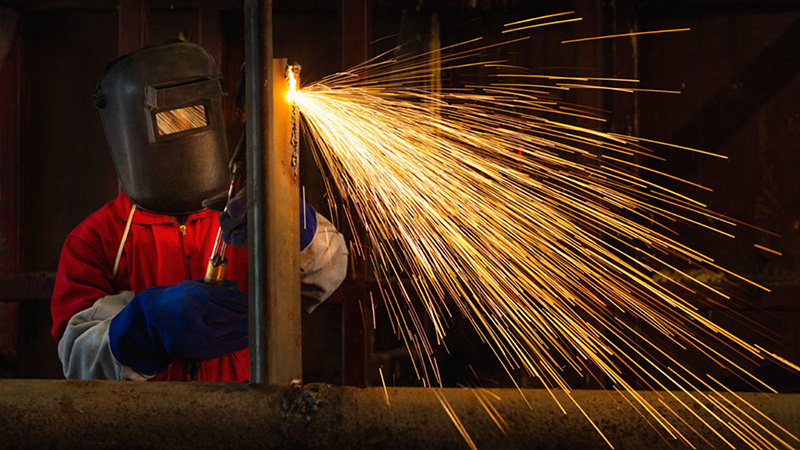
Welding Process
1.What Is Welding Chiller?
A Welding Chiller is a cooling machine that controls the temperature and pressure of the welding process by using chilled circulated water to release heat out of the system.
our welding chillers are highly cost effective and custom designed for your specific welding machine operation.
Small Welding Chiller
2.How Does Welding Chiller Work?
Welding chillers are used to cool welding equipment,which can achieve uniform and high-quality welds
Chilled water in a welding chiller is continuously passed through the heat exchange of your application and compressor refrigeration system.
Welding chillers circulate chilled water from different components and processes to dissipate unwanted heat from the welding machines.
The heat generated by your application during the welding process is driven through the cooling cycle of the refrigeration system and dissipated into the air.
The control panel of the welding chiller is responsible for controlling the cooling of the compressor according to the adjusted temperature value.
Ensure that cooling water temperatures for welding applications are controlled within set parameters.
Welding chillers provide longer welding tip life by reducing downtime in welding applications.
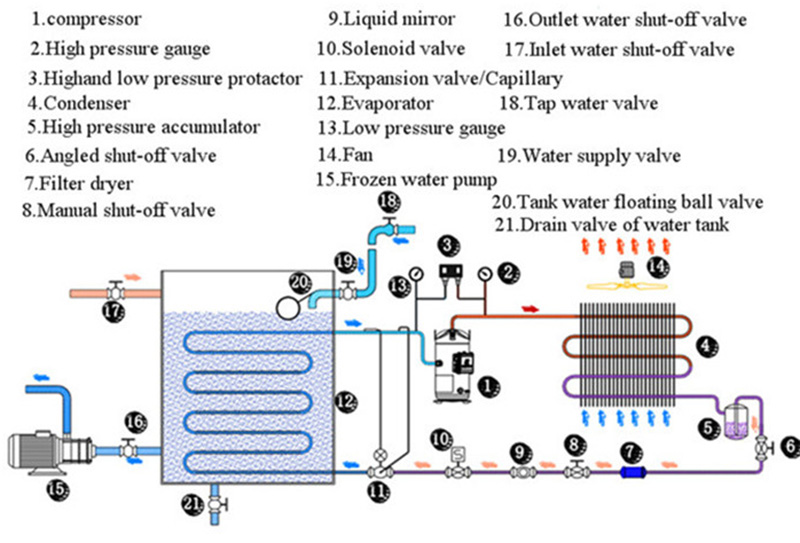
3.Why Need Welding Chillers for Welding Process?
For industrial operators performing resistance welding, the heat generated by the process can be significant and needs to be dissipated. Since the heat of the welding reaction is directly related to the amount of current applied to each weld, maintaining a stable temperature will help stabilize the current and improve the overall efficiency of the weld.
Achieving stable temperatures for resistance welding requires the use of a cooling source. Historically city water sources have been used, but more modern and efficient cooling can be achieved through the use of specialized welding machine chillers. Among the main benefits, industrial chillers and portable chillers for welding reduce long-term operational costs and promotes more accurate temperature regulation,so welding chiller can help minimize much process cost.
4.What’s the Difference Between Air-cooled & Water-cooled Welding Chillers?
There are two types of welding chiller: one is air-cooled welding chiller ,the other is water-cooled welding chiller ;
Air-cooled welding chillers use ambient air to dissipate heat from the brewing processes. They are energy-efficient, space-saving, and less maintenance that helps save money.
Water-cooled welding chillers use water from an external water cooling tower to dissipate heat from the brewing processes. These systems are longer lifespan, Relatively quiet, and more consistent cooling performance than the air-cooled welding chiller.
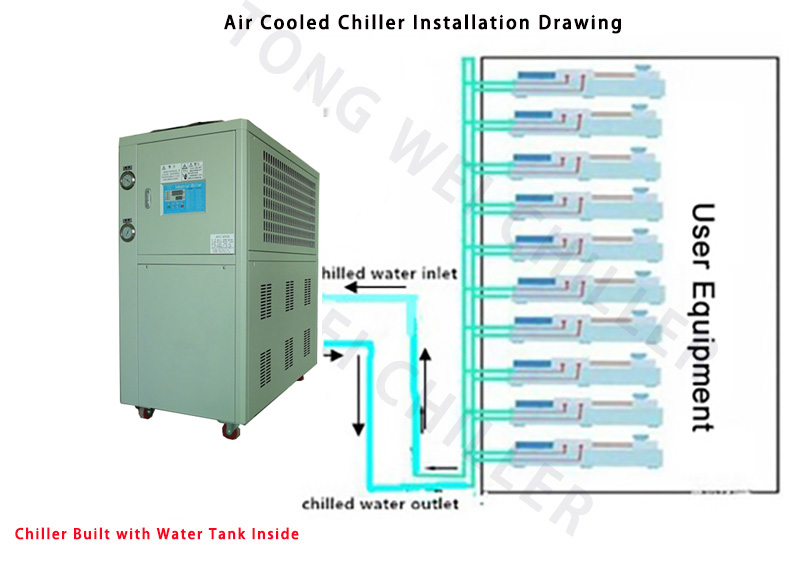
Air-cooled Welding Chiller Installation Drawing
Water-cooled Welding Chiller Installation Drawing
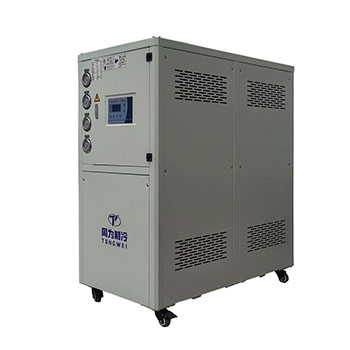
Air-cooled Welding Scroll Chiller Water-cooled Welding Scroll Chiller
Should you choose an air-cooled or water-cooled Welding chiller? Contact Us for help determining the best solution for you.
5.What Are The Main Components of Welding Chillers?
5.1 Compressor
The compressor is the key mover in water chiller because it produces pressure variations to stir the refrigerant around.
From 1/2HP(1/2 Ton) to 60HP(5oTon) waterjet cutting chiller , which is with Panasonic or Danfoss brand Scroll compressor ,
Panasonic Compressor
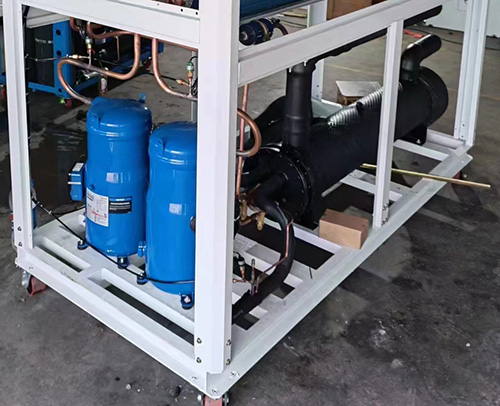
Danfoss Compressor
5.2 Evaporator
The evaporator is a crucial component of air-cooled water chiller, as it is responsible for extracting heat from the liquid being cooled,it is located between the compressor and the expansion valve. There are three types of evaporators : coil in water tank evaporator , shell and tube evaporator, 304SS stainless steel plate type evaporator.
Coil in SS Water Tank Evaporator
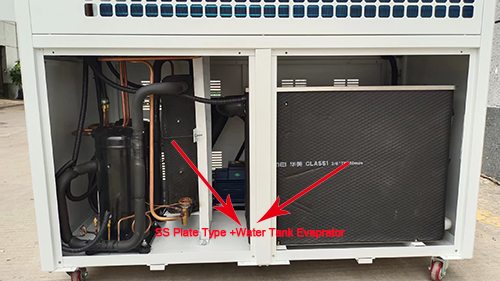
SS Plate Type+ Water Tank Evaporator
Shell and Tube Evaporator
5.3 Water Pump
The water pump is designed to increase the pressure and the flow of the chilled water in a closed space.
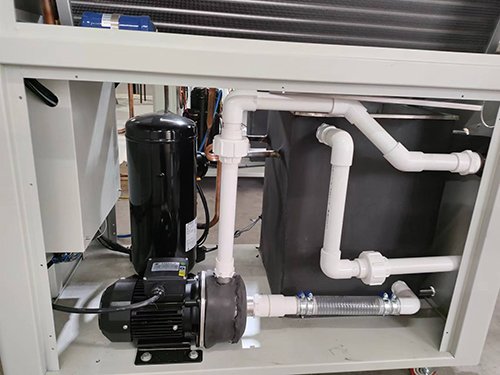
Water Pump
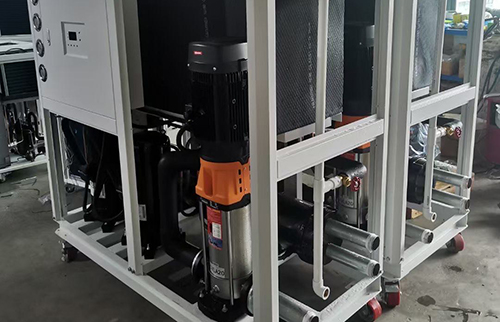
High Pressure Water Pump
5.4 Condenser
The condenser for air-cooled welding cooler is equipped with efficient cross-seam fins and female threaded copper tubes for high heat exchange efficiency and good stability.Its function is to cool down the refrigerant steam released from the compressor into a liquid or gas-liquid mixture.
Aluminum fin+fan Condenser for air -cooled welding chiller
The condenser for water-cooled welding cooler is shell and tube ,with the internal copper tubes employing an outer thread embossing process.This design effectively enhances the heat exchange efficiency between the refrigerant and water during the process. Compared to traditional smooth copper tubes, the outer thread embossing process increases the surface area of the copper tubes, thereby expanding the contact area for heat exchange and improving the thermal conductivity of the condenser. This optimization design allows the condenser of the water-cooled chiller to transfer heat from the refrigerant to the water more rapidly and consistently, enabling the water to carry away the heat.
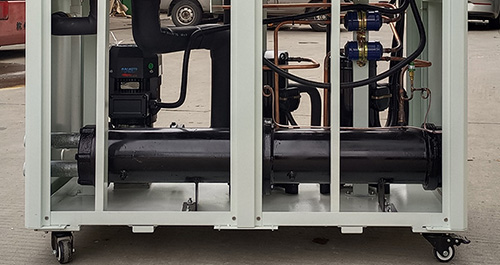
Shell and tube Condenser for water-cooled welding chiller
5.5 Controller Panel
Water chillers use precision digital temperature controller, it RS485 communication port,which can do remote monitoring and control. Simple operation, low failure rate, high safety factor, easy installation.
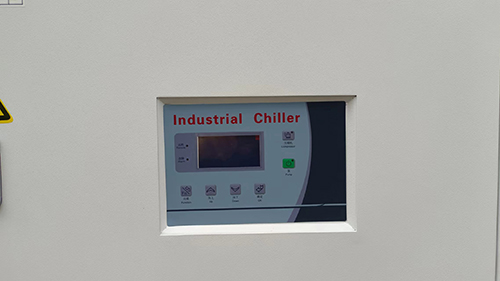
Controller Panel
6. What are the Key Features of a Welding Chiller?
▪ Energy-efficient Panasonic/Danfoss compressor
▪ 304 Stainless steel water pump
▪ Chilled 0utlet water temperature control 7℃ to 25℃
▪ Precise temperature controller
▪ Environment-friendly refrigerant R407c/r410a
▪ PID temperature controller
▪ Easy installation ,operation and low cost of maintenance
▪ 304 Stainless Steel Coil in SS water tank as evaporator
7.What are the Industrial Applications of Welding Chiller?
Welding Chiller used in several applications regarding welding processing as:Resistance welders, laser welder, seam welders, laser markings, butt welders, YAG laser, and induction welders.
Welding chillers play a vital role in the effective cooling of various welding equipment and welding processes.
Some welding applications that require a welding chiller include:
▪ laser cutting
▪ Laser welding
▪ Laser drilling
▪ Laser Marking
▪ Semiconductor laser processing equipment
▪ CO2 laser
▪ YAG laser (working medium)
▪ Steel structure manufacturing industry
▪ Automotive Manufacturing
▪ Security door processing industry
▪ Gas shielded welding applications
▪ Arc welding machine
▪ DC welding machine
8.How to Choose Right Welding Chiller for Your Welding Process?
How to calculate right cooling capacity for your welding chillers?
One of the most frequently ask about how we can know the cooling capacity for chillers.
The range of a chiller at which it can discharge heat from a heated fluid is called cooling capacity.
The cooling capacity of a laser Chiller ranges from 1/2KW to 100KW.
Let’s see the below formula.
Cooling Capacity(kw)= Flow Rate(m3/h)*Temp Change(T1-T2)/0.86
Heat Load= C(specific heat)* M(quality output per hour )*Temp Change(T1-T2)
Oversize the chiller by 20% Ideal Size in KW = KW x 1.2
Noted : T1:Incoming Water Temperature (℃) T2:Required Chilled Water Temperature(℃)
For example, what size of chiller is required to cool 5m³ water from 25°c to 15 °c in 1 hour?
Temperature Differential = 25℃-15℃=10℃
Water Flow Rate = 5 m³/hour
Cooling Capacity in KW = 5 x 10 ÷ 0.86 = 58,14 KW
Oversize the chiller = 58.14 x 1.2 = 69.76 KW
69.96kw cooling capacity for chiller is required.
Types of plasma cutting chiller system?
There are two types of chiller :Air Cooled welding Chiller and Water Cooled welding Chiller.
Water cooled chiller needs a separated water cooling tower and water cooling pump ,if you don‘t have exsiting water cooling tower,we suggest you use air cooled chiller; But if your ambiemt temperature is very high above 55℃ ,we suggest you use water cooled chiller , as it is easier to dissipate heat for water cooled chiller with water cooling tower.
Whether chillers need built-in Tank or not?
In a chiller system, a tank is usually equipped to buffer the thermal load of the chiller.
But should we choose a built-in type of tank or an external type of tank?
A chiller with a built-in tank is easier to install and can be used simply by connecting a water pipe to your application.
But it has a limited capacity and is not suitable for applications with larger chilled water demands.External tank’s capacity can be customized according to specific needs.
It can buffer a larger heat load, store more chilled water, but the installation will be more troublesome.
If you don‘t have external water tank ,we suggest our chiller built-with water tank ,which is easy for you to install.
Cooling capacity unit conversion?
1 KW=860 kcal/h ;
1 TON=3.517 KW;
1 KW=3412 Btu/h;
9.Get a Quote on Industrial Welding Chillers Now