How Many Types Of Water Chillers There Are ?
Time:2023-10-24
Views:128
Water chillers are key components in many industrial and commercial cooling systems and can be classified in various ways based on condenser type, cooling capacity, and compressor type. This comprehensive guide provides detailed insights into each category to help you make the best choice for your specific needs.
Classification By Type of Condenser
The condenser plays a vital role in the chiller system, effectively removing heat from the system. Two main types of condensers are prevalent in industry - air-cooled chiller and water-cooled chiller
Air-cooled chillers use the air surrounding the system to cool and condense the refrigerant. Ideal for small to medium cooling loads, these chiller can be located outdoors or indoor with a fan driving ambient air through a finned tube , promoting efficient heat dissipation.
Air-cooled chillers offer simpler and more cost-effective installation and do not require a separate cooling tower or condenser water pump. They have relatively low maintenance requirements, but they tend to have higher power consumption and potentially shorter lifespans than their water-cooled counterparts.
In contrast to air-cooled chillers, water-cooled chillers utilize cooling towers to increase thermodynamic efficiency. Typically used in large commercial buildings or industrial facilities, these coolers effectively manage large-scale cooling applications.
In these systems, the waste heat generated by the chiller is dissipated to the atmosphere through a cooling tower. This process involves the evaporation of water under low pressure, promoting efficient heat absorption.
Water-cooled chillers, while offering superior energy efficiency and quieter operation than air-cooled chillers, require regular maintenance. This includes treating the condenser water to prevent the growth of microorganisms and minimize the accumulation of mineral deposits. However, they are a good choice for applications where heat recovery systems can utilize the rejected heat. Air-cooled chillers offer simpler and more cost-effective installation and do not require a separate cooling tower or condenser water pump. They have relatively low maintenance requirements, but they tend to have higher power consumption and potentially shorter lifespans than their water-cooled counterparts.
Classification By Cooling Capacity
The cooling capacity of a chiller is a key parameter that determines its suitability. Measured in KW ,tons, Kcal/h or British Thermal Units (BTU) per hour, cooling capacity represents the amount of heat a chiller can remove from a process in a specific amount of time. Chillers are generally divided into the following categories:
Small Capacity Chiller
Small capacity chillers, with cooling capacities ranging from 0.2 tons to 20tons, are compact and often portable. These chillers are ideal for small applications such as laboratory cooling, small scale manufacturing processes, medical applications, food and beverage industry cooling requirements, and more.
Medium Capacity Chiller
Refrigeration capacities range from 20 to 200 tons, with medium-sized chillers suitable for larger commercial applications. These include building HVAC systems, industrial cooling processes,and more.
Large Capacity Chiller
Large capacity chillers, providing over 210 tons of cooling capacity, are typically designed to address large industrial applications and district cooling systems. Given their size, these chillers are often customized to the specific requirements of the application.
Classification By Compressor Type
Depending on the compressor type, chillers can be classified as reciprocating chiller, scroll chiller, screw chiller, and centrifugal chiller.
Reciprocating Chiller
Reciprocating chillers use a reciprocating compressor that operates similar to a car engine. the refrigerant is compressed by the back and forth movement of the piston inside the cylinder. Reciprocating compressor chillers are typically used in small to medium-sized cooling applications.
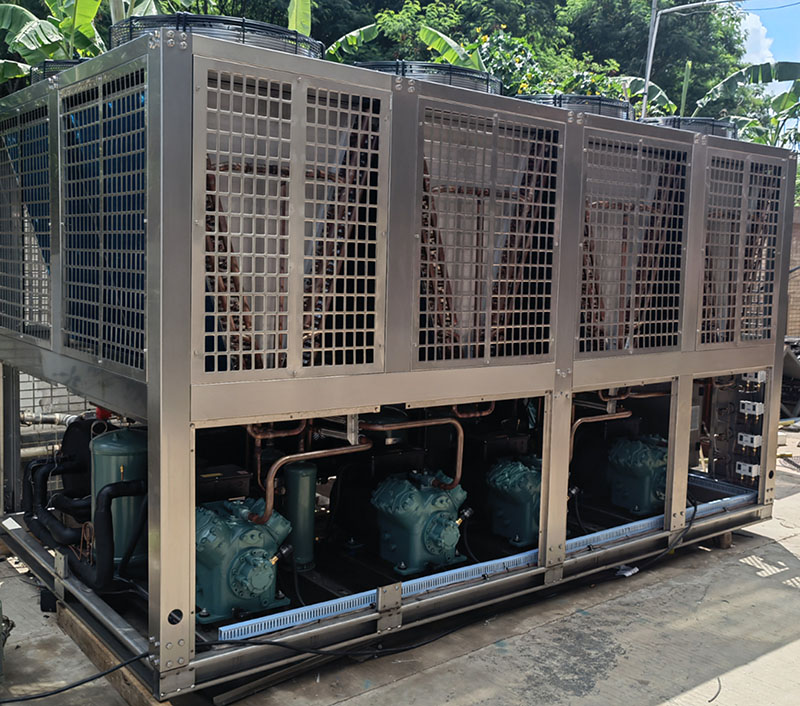
Scroll chillers use scroll compressors, which features two interlocking spiral components that rotate together to compress the refrigerant. When one vortex remains stationary and the other orbits, the refrigerant is forced toward the center, creating compression. Scroll chillers offer quiet operation, superior efficiency and exceptional reliability, making them a popular choice for small-sized cooling chiller needs.
Screw chillers use screw compressors, which features two intertwined spiral rotors enclosed in a housing. As these rotors spin, there is less space for the refrigerant, causing compression. Due to their high efficiency and reliability, screw chillers are often chosen for large-scale commercial and industrial applications.
Centrifugal Chiller
Centrifugal chillers use centrifugal compressors to compress the refrigerant by rotating a high-speed impeller. These coolers are ideal for large cooling loads as they can achieve large amounts of cooling capacity while maintaining high efficiency.
there are a variety of chillers, each with unique features and benefits, offering countless options to meet a wide variety of cooling requirements. Whether you need a compact portable chiller for a small application or a custom high-capacity chiller for an industrial process, understanding these classifications can guide you in making the best choice for your specific needs.